Work Order Entry
Purpose
Create Work Order documents. Documents are posted to GL on closure. Advanced Manufacture is used when we wish to add items and costs to the BOM during the manufacturing duration.
Procedure
- Select the type of Work Order, (Assemble and Unassemble have similar settings)
- Select the item by either entering the Item Code or by selecting through the item description from the drop-down list
- Select the Destination location of the work order
- Set the Quantity of the item
- Set the Date of the Work Order
- Enter the Labour Cost if applied
- Select the Credit Labour Account from the Drop-down list
- Enter the Overhead Cost if applied
- Select the Credit Overhead Account from the drop-down list
- Enter associated notes in Memo
- Click Add Workorder
- Note: Assemble and Unassemble are practically two opposite actions
- Select the item by either entering the Item Code or by selecting through the item description from the drop-down list
- Select the Destination location of the work order
- Set the Quantity of the item
- Set the Date of the Work Order
- Set the Required by Date of the work order
- Enter associated notes in Memo
To Assemble or Unassemble
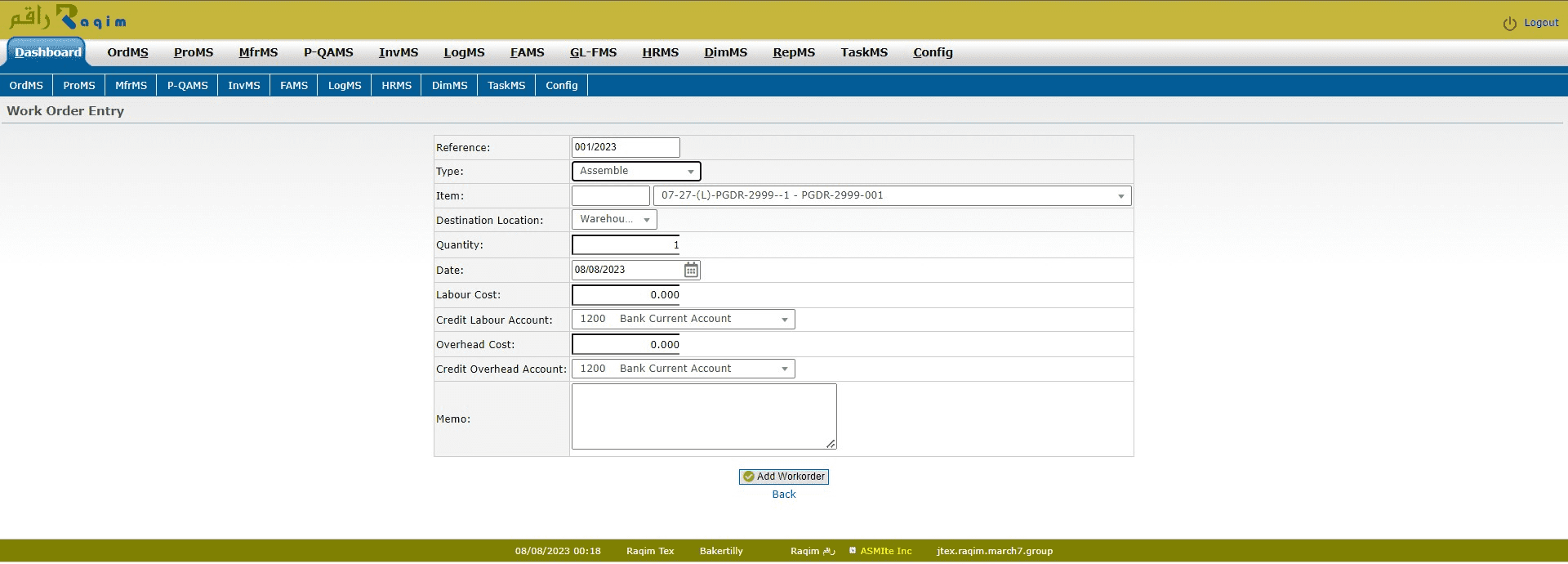
For Advanced Manufacture
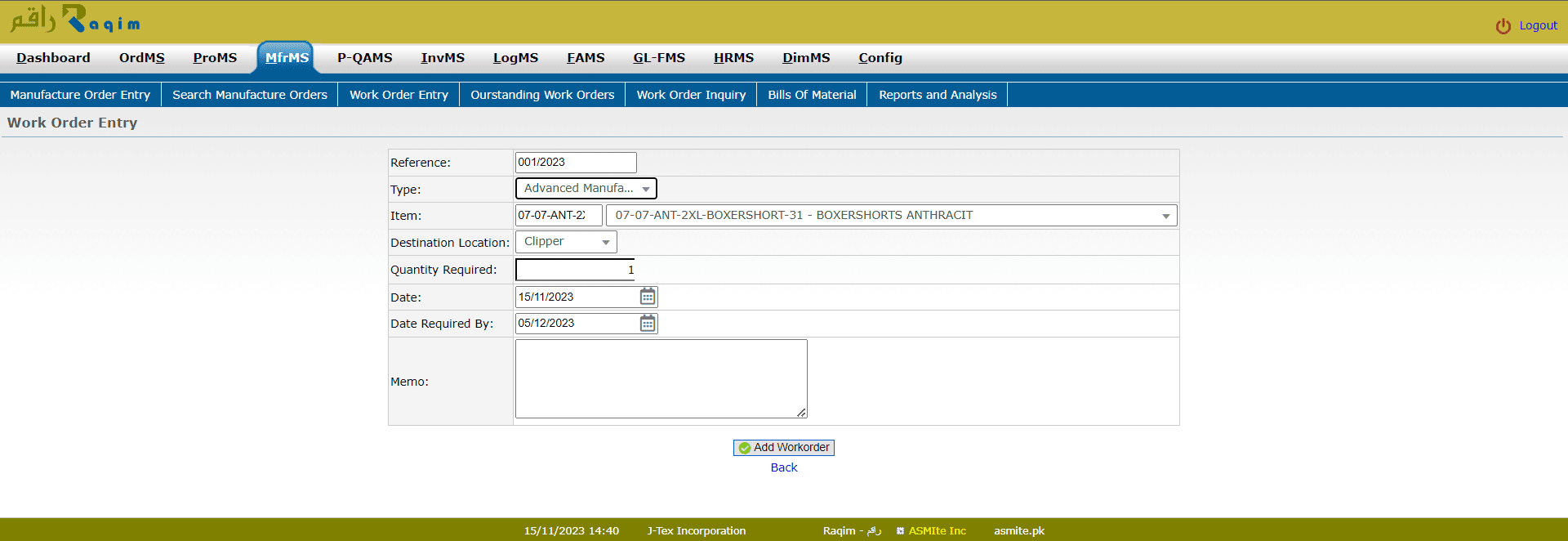
Tips and Tricks
- Set a Bills of Material for a manufactured Items before creating a Work Order.
- Make sure appropriate Item Assembly Costs Account is set in System and General GL Setup.
- Work Order Required by setting defines number of days to allow for manufacturing of items.